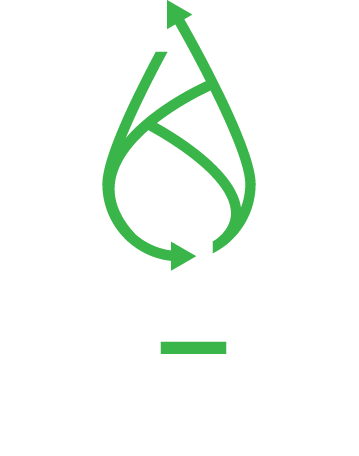
GReTa
Initial situation:
The Renewable Energy Sources Act has been promoting the energy turnaround to reduce environmentally harmful fossil energy resources for over 20 years. Wind energy plays a key role in this, with the number of wind turbines growing every year. The trend towards ever larger wind turbines and rotor blades is leading to a considerable increase in the amount of materials and raw materials required to build the turbines. After an average service life of 20 years, the question of recycling and closed material cycles has not yet been sufficiently clarified. Dismantled wind turbines are predominantly thermally recycled, landfilled (USA) or occasionally find secondary use in furniture or works of art.
The project:
With the help of pyrolysis, it is possible to separate the resin-fiber system and extract new raw materials from the resin. The fibers can in turn be used for new wind turbines. The challenge here is the nature of the resin, which often consists of thermosets and therefore makes processing difficult. In addition, a certain degree of fiber purity must be achieved so that they can be spun again.
Goals:
The overarching project goal of a closed material cycle includes the development of a new and innovative rotor blade design. The decisive factor here is the consideration of recycling in the design of the rotor blade (Design 4 Recycling). If possible, this should be constructed using only carbon fibers for reinforcement. In addition to the very high specific properties, economic recycling by pyrolysis is already possible today. In this context, an improvement in the use of raw materials is to be achieved by further developing the recycling process. In addition to the carbon fibers, the matrix is also to be collected as pyrolysis oils during fiber-matrix separation. To this end, AES is developing a new infeed module and optimizing the yield and quality of the pyrolysis products. These recycling products will then be used to create new semi-finished fiber and matrix products for automated rotor blade production. The decisive advantage therefore lies in the
closed material cycle over the entire product life cycle.
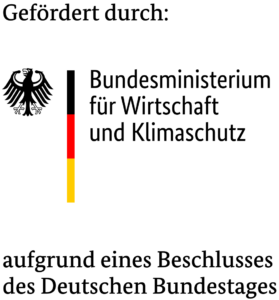